RISE’s innovative patent: Green Positive?
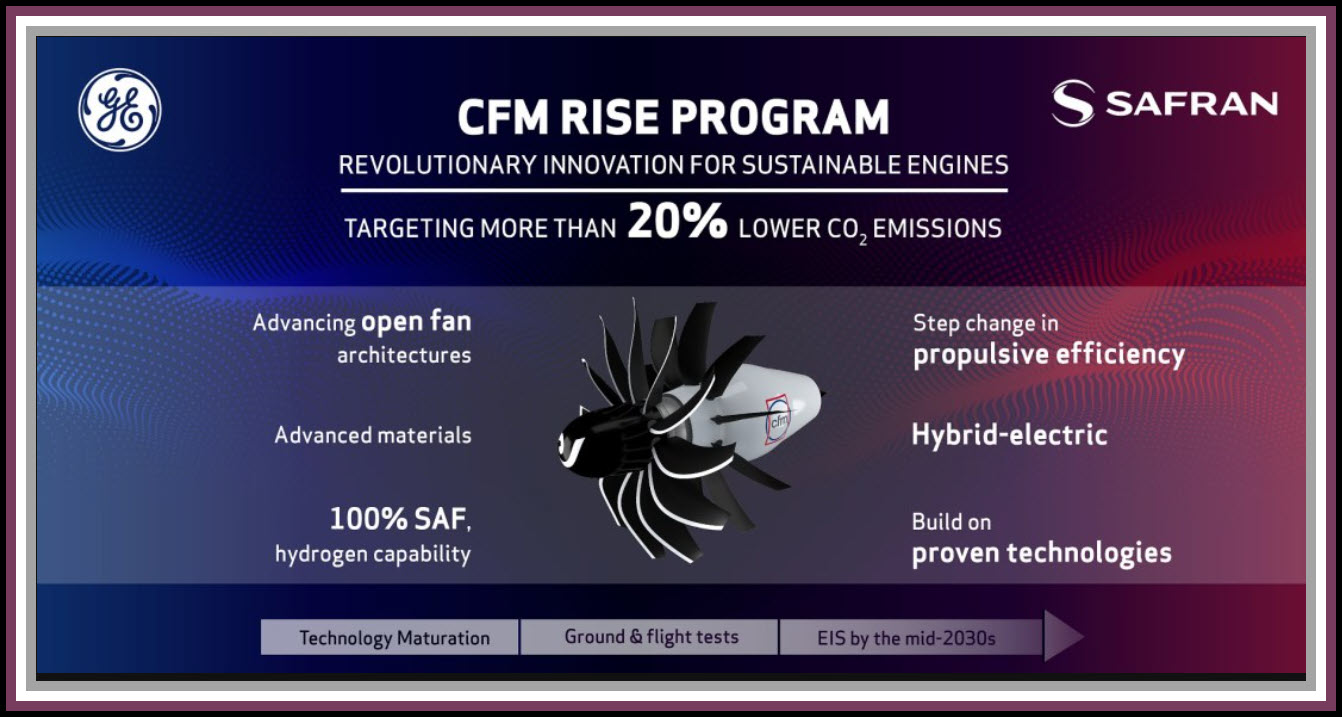
The 2050 Global Net Zero Carbon Emissions Goal is a challenge that requires all in aviation to pursue all possible solutions that might reach this goal. This target qualifies as Long-Term Aspirational Goal. This target was formally adopted by ICAO Member States during the 41st ICAO Assembly in October 2022.
Options being studied include these initiatives, among others:
- Advanced Aerodynamics: Blended wing bodies, canard wings, and truss-braced wings to reduce drag and improve lift-to-drag ratios.
- Lightweight Materials: Increased use of composites and advanced alloys to reduce aircraft weight.
- Geared Turbofan Engines: Improve fuel efficiency by 15–25% over current models.
- Open Rotor & Ultra-High Bypass Engines: Like the RISE engine, designed to cut fuel burn and emissions by up to 20%.
- Hybrid-Electric Propulsion: Combines combustion and electric systems for improved efficiency during different flight phases.
- Fully Electric Aircraft: Zero-emission operation using battery or fuel cell power; viable for short-haul and regional flights.
- Hydrogen Combustion & Fuel Cells: Offers high energy density and zero CO₂ emissions, though infrastructure and storage remain challenges.
- Bio-based SAF: Derived from waste oils, algae, or agricultural residues.
- Power-to-Liquid (PtL) SAF: Synthesized using renewable electricity and captured CO₂.
- Blending Mandates & Incentives: Governments are introducing SAF quotas and subsidies to scale production.
- Optimized Flight Paths: Improved air traffic management systems like Single European Sky and U.S. NextGen reduce fuel burn.
- Weight Reduction Strategies: From lighter cabin materials to stricter cargo limits.
- Fuel-Efficient Taxiing & Climb Profiles: Pilot training and automation help minimize unnecessary fuel use.
None of these has reached a point where it is clear that it may be the answer. In fact, some think that a multi-prong approach may be the key. Flight Global has published (below) an article analyzing the patent filed for the Safran/CFM/GE’s RISE project
The RISE engine—short for Revolutionary Innovation for Sustainable Engines—is a next-generation open rotor propulsion system under development by CFM International, a joint venture between GE Aerospace and Safran Aircraft Engines. While the full patent portfolio is still emerging, several filings and technical disclosures offer a glimpse into its groundbreaking architecture.
- Single-stage open rotor design: Unlike earlier contra-rotating concepts, RISE uses a single rotating fan followed by variable-pitch stator vanes, which can nearly close to act as an air brake—eliminating the need for a thrust reverser.
- Recuperator system: Captures waste heat from exhaust gases to preheat compressed air before combustion, improving thermal efficiency.
- Noise reduction features: Patents include serrated stator blades, swirl recovery vanes, and rotating FOD protection systems to address the acoustic challenges of open rotor engines.
- Modular fan gearbox: Designed for easier maintenance and integration with hybrid-electric systems.
- Swirl recovery vanes (SRVs) are a key aerodynamic feature in open rotor propulsion systems like the RISE engine, designed to redirect rotational flow into axial thrust.
- The SRVs positioned directly behind the propeller blades
- Their fixed-pitch, slightly tapered design using NACA 16-series airfoils
- How they interact with the propeller’s slipstream to recover swirl and improve efficiency
- The SRV blade geometry
- Flow visualization of swirl reduction
- Efficiency gains across different thrust coefficients
The RISE engine is expected to move the needle towards the 2050 goal by reducing fuel burn and CO₂ emissions by 20% compared to current LEAP engines; its Compatibility with 100% Sustainable Aviation Fuel (SAF) and potentially hydrogen. This is an encouraging prospect but as with any new technology, the time between initial positive results and proof of its potential can involve years of testing and implementation plus the path is fraught with problems.
Safran patent filings offer glimpse of potential details on next-generation RISE engine
By Dominic Perry9 July 2025
A series of recent patent filings from Safran Aircraft Engines (Safran) could hint at some of the innovations being contemplated for the RISE open-rotor engine the French firm is developing alongside GE Aerospace in their CFM International joint venture.
Swirl recovery vanes with saw-tooth profiles for noise abatement, protective blades to “chop” foreign object debris, and even an “optimised” fan system that features a reduction gearbox between it and the low-pressure spool, are all highlighted in the documents.
Source: CFM International
RISE open-rotor engine is seen as a solution for the next generation of narrowbody propulsion
In addition, while ostensibly covering the entirety of an unducted fan engine, another filing contains detailed, although broad, specifications for the size and profile of the swirl recovery vanes – also referred to as stator blades – that sit behind the fan.[1]
These are critical to the performance of the open-rotor engine, the patent filing says, as they both “straighten” the airflow from the fan to generate thrust and help to limit overall aerodynamic losses from the combination of the two components through the “recovery of the rotating airflow downstream of the propeller”.
Without the swirl recovery vanes “this rotating flow would be responsible for significant aerodynamic losses, leading to a significant degradation of thrust and therefore of the propulsion system’s efficiency,” it adds.
The vanes – of which there should be fewer than the number of fan blades, it states – also adapt the airflow to account for other components installed around the engine, such as the pylon “to ensure the operability and performance of the installed propulsion system”.
This could be achieved through “different geometries” depending on the location of the stator blades.
On top of which, the shape of the blades is vital to minimise the noise created by the interaction of the airflow from the fan and its tip vortices with the swirl-recovery system.
A flat blade or one whose leading edge is too thin are viewed as particularly problematic, the patent filing says.
Noise abatement is the chief goal of another patent claim, which proposes stator blades with saw-tooth profiles on their leading edges.
Interaction of the successive rows of blades can “generate noise emissions”, the filing says, and the absence of a nacelle on an open-rotor design “permits the direct diffusion of this to the environment”.
But if the leading edge of the stator blades feature a serrated profile – this should have at least three teeth, one of which should be inclined – this helps to reduce the noise produced and limit aerodynamic losses, the patent claims.
“With more inclined teeth, and therefore more pronounced leading edge sweep angles, near the blade tip, it is possible to better eliminate the negative effects of interactions with the blade tip vortices of the [fan blades], in the region where they will be most significant,” it adds.
Although illustrations accompanying the patent filing also shows serrated profiles on the trailing edges of fan blades, there is no mention of this embodiment in the claim itself.
Source: Safran Aircraft Engines/European Patent Office
Serrated blade profiles are designed to reduce noise levels from unducted engine
If NOISE is one concern of the open-rotor design, then the ingestion of FOD is another, a hazard to which the engine type is “most exposed”, one of the filings notes.
It proposes an array of blades mounted aft of the fan but in front of the swirl recovery vanes.
These would rotate along with the fan, providing them with “a centrifugal effect” which would “cut or chop any foreign body such as ice or volatile matter” reducing the size of material that could be ingested into the engine core.
The rotation of the blades would also “centrifugally drive the foreign body radially outward, and away from the inlet of the primary flow path.”
As an added benefit, the blade configuration “can influence the airflow exiting the rotor blades and improve the turbomachine’s performance,” it adds.
“In particular, the blade profile is combined with the rotor blade pitch to achieve the equivalent of a variable cycle.”
While still officially only a demonstrator, the RISE design, which should cut fuel burn by more than 20% compared with current state-of-the-art engines, is being heavily touted as the propulsion solution for the next generation of narrowbody aircraft.
As with previous CFM products such as the CFM56 and Leap powerplants, Safran Aircraft Engines is responsible for the low-pressure and fan systems on the RISE, while GE looks after the high-pressure system.
Although a patent application is no guarantee that a technology or system will end up on an in-service product, they do offer a glimpse of which advances a company thinks may have potential.
Interestingly, while CFM has consistently maintained that most of the fuel-burn reduction on the RISE will be delivered through the improved propulsive of the open-rotor design and the better thermal efficiency of the core, several of Safran’s patent applications reference the use of a reduction gear to decouple the fan’s rotational speed from that of the low-pressure spool.
Indeed, in one document – titled Aeronautical propulsion system comprising an optimised fan system – the filing notes that the use of a REDUCTION GEAR is a key means of achieving the high bypass ratios required for the next generation of engines.
The optimised fan design presented incorporates such a reduction mechanism and is described as applicable for both ducted and unducted use cases.
“This decoupling reduces the rotational speed and pressure ratio of the fan rotor and increases the power extracted by the low-pressure turbine,” it says, increasing the overall propulsive efficiency of the system.
[1] Swirl recovery vanes (SRVs) are a key aerodynamic feature in open rotor propulsion systems like the RISE engine, designed to redirect rotational flow into axial thrust. The SRVs positioned directly behind the propeller blades. Their fixed-pitch, slightly tapered design using NACA 16-series airfoils. They interact with the propeller’s slipstream to recover swirl and improve efficiency. The SRV blade geometry. Flow visualization of swirl reduction. Efficiency gains across different thrust coefficients.